Thema: Sd.Kfz 9 FAMO 1:10 Baubericht (früher 1:16) |
[ - Antworten - ] |
20.10.2014, 17:32 Uhr
 Stahlsturm
(steelfire)
|
Hallo Matthias,
schön von dir und deinem Projekt zu hören. Bei deiner Recherche nach den Reifen-Details hätte ich helfen können wenn mir die Problematik bekannt gewesen wäre. Alles kein Drama! Auch wenn ich stark geizig bin mit Bildern und Unterlagen die ich gesammelt habe aber jemand der SO baut wie Du, dem helfe ich doch gern.
Beste Grüße,
Falk
|
|
|
|
|
07.02.2015, 15:44 Uhr
 panzerpabst

|
Hallo Leute,
es gibt mal wieder ein kleines Update meines Projektes.
@Hartmut, der Baustaub deines Wanddurchbruchs hat sich offenbar nicht auf deine Augen gelegt, die etwas zu dicke Zick-Zack-Lamelle ist eines der Details die noch überarbeitet werden sollten. Die Unstimmingkeit ist dir ja gleich aufgefallen.
In der Zwischenzeit habe ich mal ein paar Probefragmente des Reifenmodells erstellt um mal zu sehen was im 3D-Druck an Details rüber kommt. Tom hat mir nach Prüfung schon mitgeteilt, dass die Beschriftung kaum gedruckt werden wird. Bei Shapeways habe ich mal 2 Teile mit deren detailliertestem Material drucken lassen.
Hier die Ergebnisse:
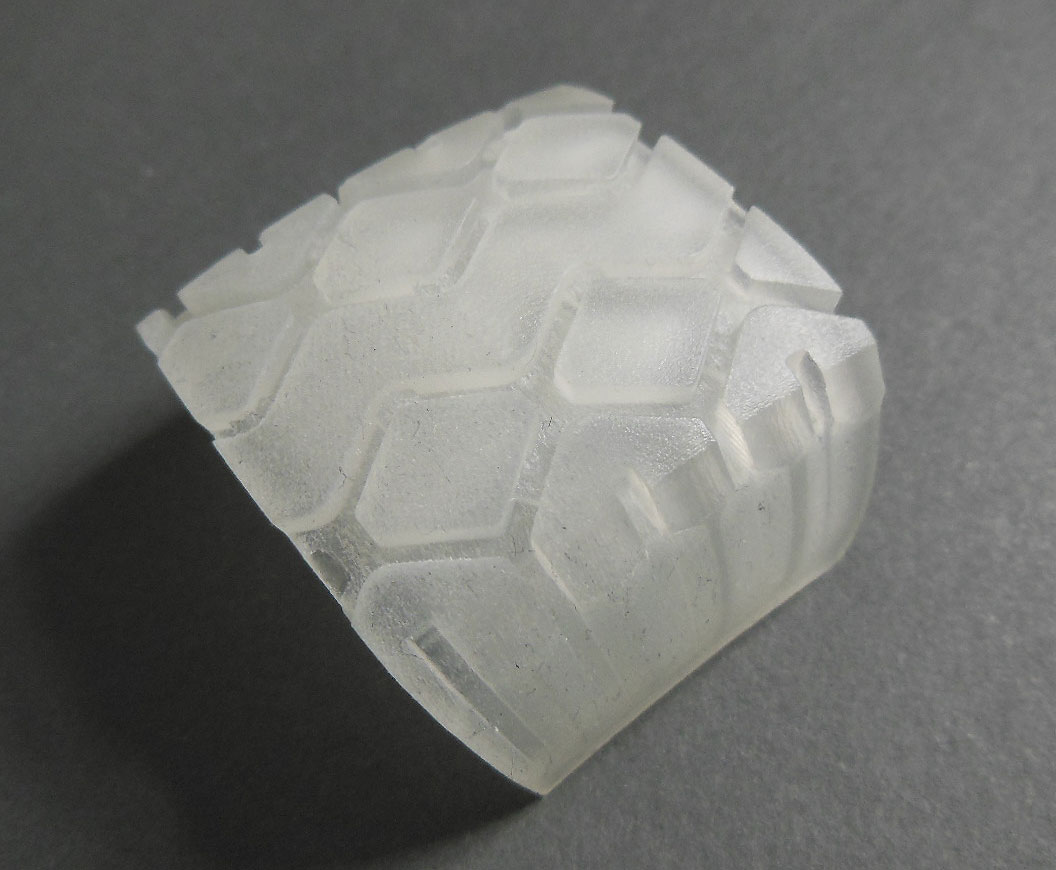
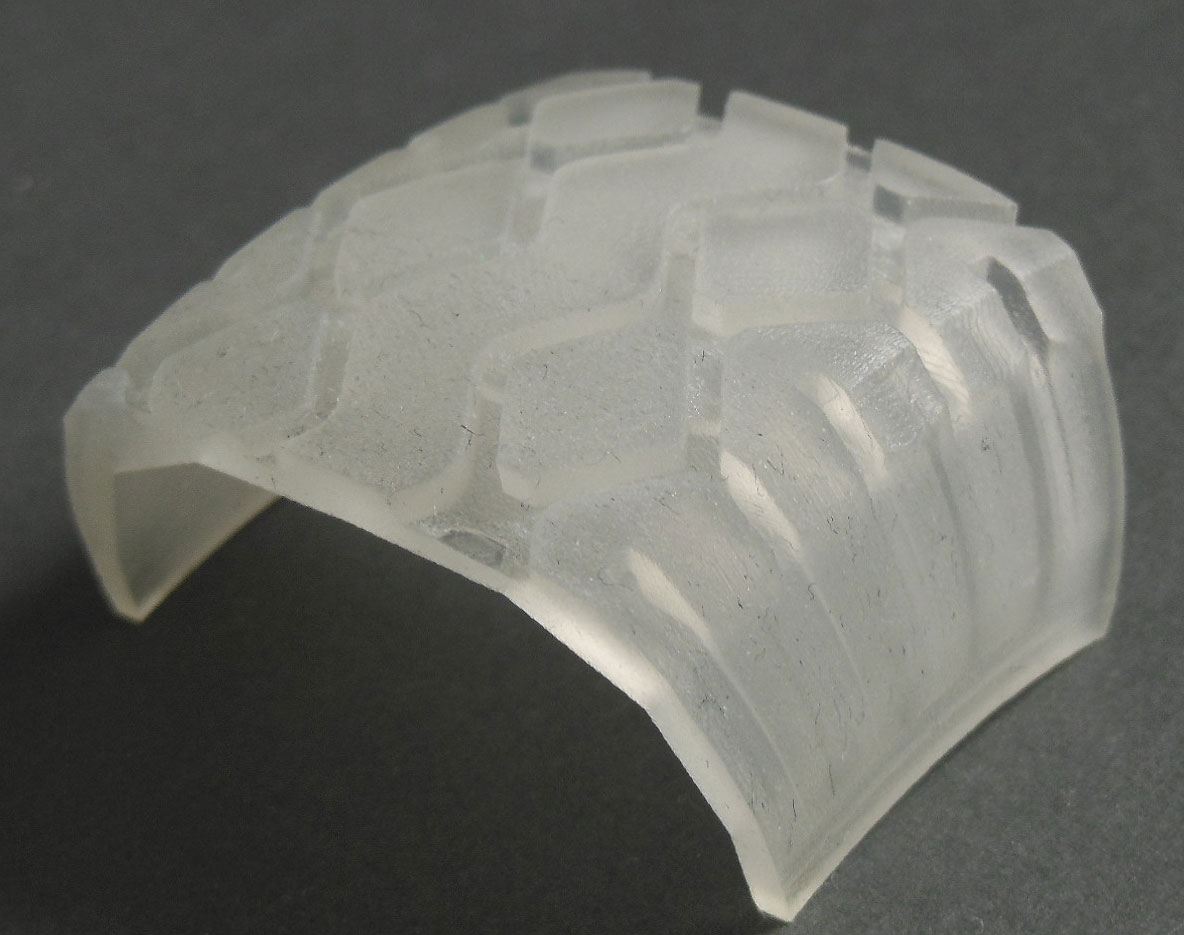
Mit dem Reifenprofil bin ich eigentlich ganz zufrieden, Rundungen kommen rund rüber und Details sind zufriedenstellend.
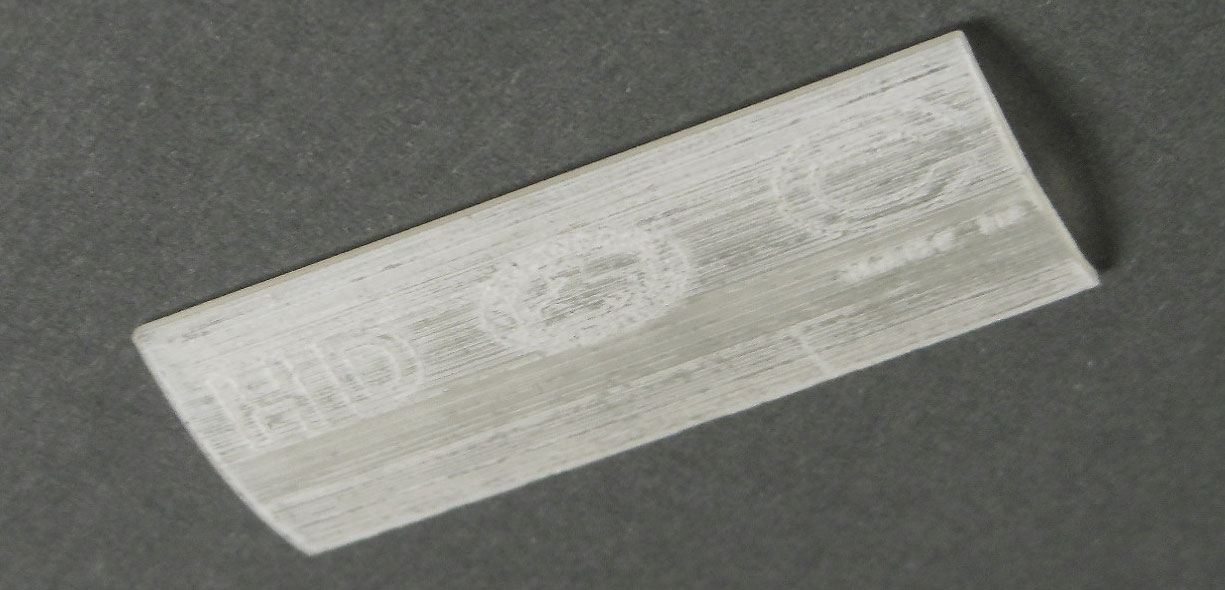
Aber wie bereits befürchtet kommen die Beschriftung und Details der Seitenwand kaum rüber. Man sieht mit Mühe die Schrift, aber als erhabene Struktur ist sie nicht ausreichend ausgebildet.
Bisher habe ich keine Lösung für das Problem, ein besseres 3D-Druckverfahren habe ich bisher nicht gefunden. Ich denke noch etwas über Fotoätzen der Schrift nach aber das wird ja auch eine unendliche Fummelei.
Um mit dem Projekt vorwärts zu kommen hab eich mich an die Erstellung von weiteren 3D-Modellen gemacht.
Mit den Modellen will ich die Kosten für das Gießen ermitteln.
Das folgende Teil ist die Halterung der Blattfeder.
3D kostet unter 10 EUR aber die Erstellung der Form kostet ca 80 EUR.
Jedes in Messing gegossene Teil würde ca 5 EUR kosten und man braucht 2 pro Famo.
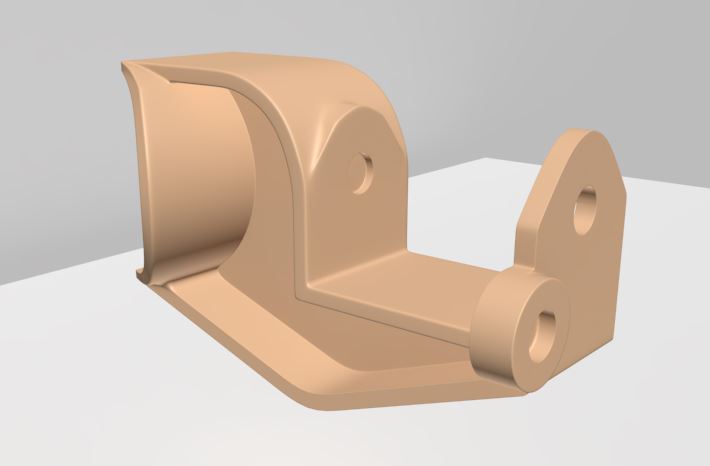
Nun kann ich abwägen ob ich das Geld ausgebe und schnell an gute Teile komme oder ich die Fräse anwerfe. Allerdings gibt es ja recht viele solcher Teile die verlockend für den 3D-Druck und das Gießen wären. Hier kamen dann mal Gedanken zu einem Gemeinschaftsprojekt hoch. Habe aber keine Ahnung ob sowas funktioniert.
Jetzt werde ich erst mal das Kettenglied als 3D-Modell fertig machen denn das soll auf jeden Fall gegossen werden - die Kosten der Form verteilen sich ja schön auf die Kettenglieder...
-- Grüße aus Leipzig
Matthias
www.boorad.de
|
|
|
|
|
07.02.2015, 17:12 Uhr
Morog
|
Hallo Matthias,
zu deinem Schrift/Reifenproblem: Warum legst du den Teil mit der Schrift nicht als Losteil aus? Dann könntest du dir zuerst ein negativ gravieren (lassen) und davon dann ein Positiv abgießen. Dieses wiederum in die Form für den Reifen einpassen und mit abgießen. Wenn das sauber passt ensteht auch kein oder minimalst Grat am Reifengummi.
Nur so ne Idee...
Gruß
Sascha -- Falle, klapp, für Kleintier grau, beweglich.
|
|
|
|
|
07.02.2015, 22:56 Uhr
 chrisch

|
Hallo Matthias,
vielleicht solltes du wirklich eine andere Formvariante wählen.
Ich würde zwei Scheiben für die Seiten drehen und die Schrift eingravieren.
Zwischen den Seitenscheiben kommt ein Ring. Das Profil der Lauffläche würde
ich auf ein Stück "Plastik" fräsen und dieses dann in den Ring einkleben.
Die Lauffläche könnte man natürlich auch im 3D-Druck herstellen.
Die Schrift wurde bei mir 1A abgebildet beim Reifenguss mit dieser Methode.
--
MfG Chrisch
|
|
Beitrag 1 mal editiert. Zuletzt editiert von chrisch am 07.02.2015 22:57.
|
|
|
08.10.2017, 17:00 Uhr
 panzerpabst

|
Hallo zusammen,
wegen des Reifens bin ich mittlerweise ganz optimistisch, mit 3D-Druck einen brauchbaren Prototypen für die Formerstellung zu erhalten.
Das Thema Machbarkeit des Kettengliedes ist nach wie vor in Prüfung. Um auch die Maße des Gliedes an das Antriebsrad anzupassen habe ich dieses inzwischen auch modelliert.
Da die Kettenglieder nicht direkt auf dem Antriebsrad laufen sondern auf Gummipolstern, musste ich diese auch gleich modellieren:
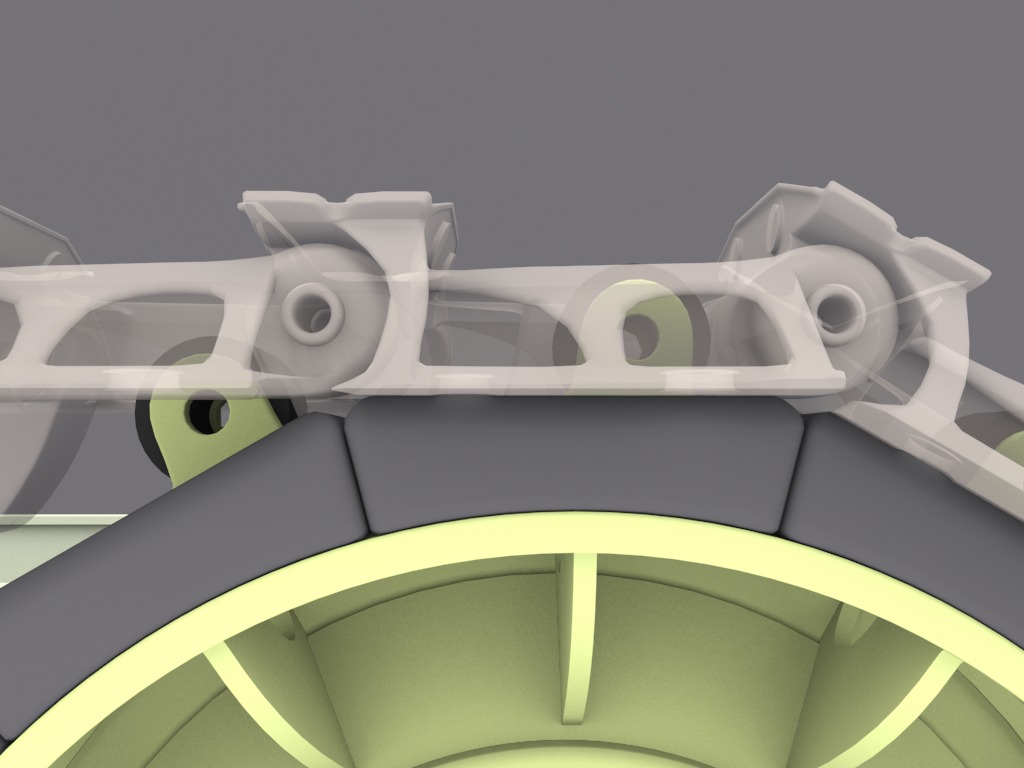
Hier musste darauf geachtet werden, dass die Rollen ab dem Kontaktzeitpunkt ordentlich an der Front des Kettengliedes entlangrollen. Da das von mir verwendetet 3D Studio Max eine Animationssoftware ist, kann man das auch simulieren.
Video
Da ich nun schon mal am Antriebsrad war und es mich schon lange gereizt hat, habe ich es gleich erstens vom Optischen soweit rund gemacht und es funktional ausgestaltet. D.h. ich habe die notwendige Mechanik so entworfen wie es passen könnte. Dazu musste ich eine Lösung finden, wie ich die 8mm Triebradachse starr am Rahmen befestigen kann. Das wird nun mittels Spannring erledigt der dann am Rahmen mit einer Schraube fixiert wird. Passende Zahnräder habe ich mir bei Maedler rausgesucht. In das große müssen auf jede Seite ein Lagersitz und auf der flachen Seite Gewinde geschnitten werden. Dort kommt das das Triebrad dran. Dazu musste auch gleich das Triebradgehäuse gestaltet werden welches aus einem oder zwei klassisch gedrehten Teilen besteht die dann noch etwas nachgearbeitet werden müssen. Überall noch Abstandhalter rein und so sollte es eigentlich funktionieren. Zwischen Antriebsrad und großem Stirnrad könnte mir noch zu viel Schmutz rein kommen. Da soll noch ein Deckel dazwischen.
Hier mal eine Schnittansicht:
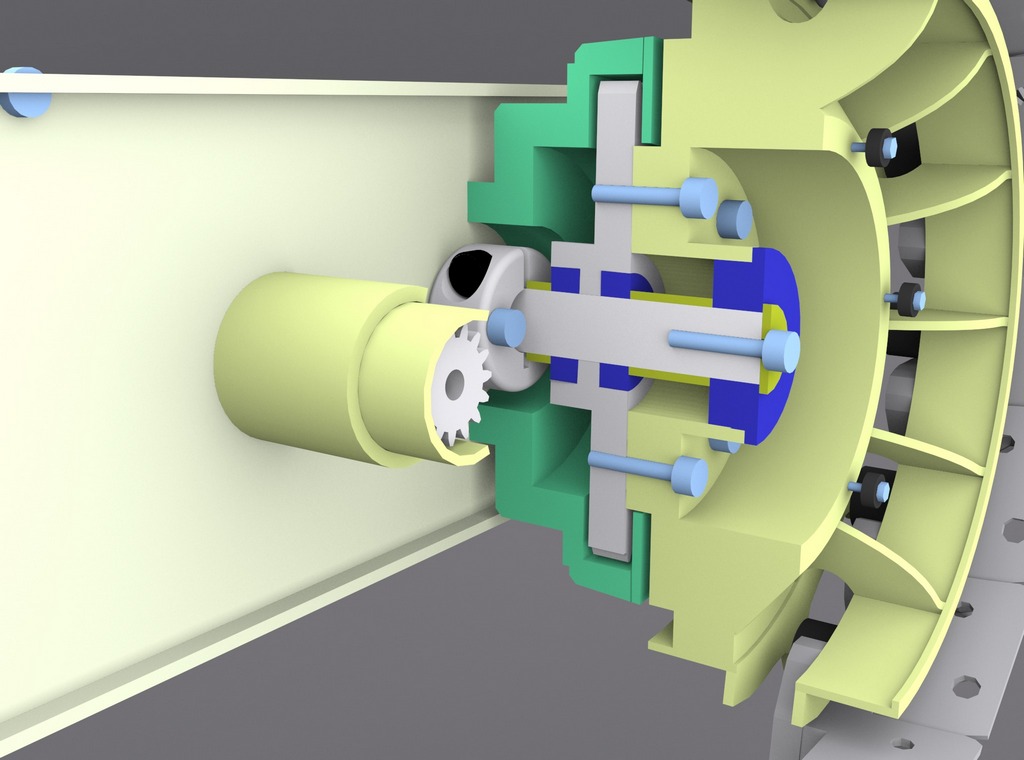
Die Fertigung des Triebrades hängt nicht unwesentlich vom Interesse an einem Gemeinschaftsprojekt ab. Dazu habe ich ja eine extra Anfrage hier und in anderen Foren laufen.
Das wars erst mal für heute.
--
Grüße aus Leipzig
Matthias
www.boorad.de
|
|
Beitrag 1 mal editiert. Zuletzt editiert von panzerpabst am 19.10.2017 20:35.
|
|
|
08.10.2017, 18:08 Uhr
 Noid
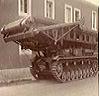
|
Wahnsinn, das sieht für mich schon fantastisch aus.
Freue mich die weiteren Bauabschnitte zu sehen.
Gruß Florian
|
|
|
|
|
09.10.2017, 17:04 Uhr
 halbkette

|
Hallo Matthias,
schöne Bilder hast du wieder gezeigt. Auf diese - bei mir nicht übliche - Weise kann man eine Konstruktion in einer einzigen Darstellung erfassen.
Das sieht schon recht kompliziert aus, was diese "versteckte Stelle" des Modells an Technik und Überlegung verbirgt. Aber so ist es ja immer - egal wo man an diesem Modell hinschaut.
Du läßt es langsam angehen, aber es freut mich schon, dass du hierbei immer noch am Ball bleibst.
Ich weiß, dass es für diese Konstruktion kaum ein Vorbild gibt und viele der Einzelheiten selbst zusammen gereimt werden müssen - mir geht es jedenfalls oft so. Dein Ergebnis gefällt mir aber sehr gut, vielleicht bis auf eine Kleinigkeit.
Laß dir doch bitte spontan einen Tip zur Konstruktion der Montage-Stelle des Antriebsrades anbieten:
Die einzige Zentrierungs-Möglichkeit für das Rad auf der Antriebswelle ist offenbar die blaue Abschluß-Scheibe mit der Zentral-Schraube in der Welle.
Ich gehe mal davon aus, dass du nicht möchtest, dass das Antriebsrad sichtbar unrund läuft - das würde aber bei der vorliegenden Anordnung unvermeidlich sein, weil immer ein entsprechendes Spiel in den Teilen und Bohrungen vorhanden ist. Deshalb schlage ich vor, dass du "zwischen großem Zahnrad und der Kettenrad-Nabe" eine Zentrier-Möglichkeit in Form eines kleinen Absatzes einrichtest.
Nur das kann dabei wirklich helfen.
Ansonsten: weiter so und viel Erfolg!
Deine Bilder sind eine gute Ablenkung von meinen Problemen... -- Gruß Hartmut
\\\\\\\" Ein Modell ist mehr als nur die Summe seiner Teile \\\\\\\"
|
|
|
|
|
06.06.2023, 14:20 Uhr
 panzerpabst

|
Hallo zusammen,
aus gegebenem Anlass habe ich mal meinen alten Baubericht unter einer dicken Staubschicht hervorgekramt.
Hartmut, deinen letzten Beitrag will ich nicht unkommentiert lassen, obwohl es nun schon fast 6 Jahre her ist. Danke für die lobenden Worte und den Hinweis zur Zentrierung.
Letztes Jahr hatte ich mal wieder einen Runden. Diesmal mit einer Zahl vorne, die mich ernsthaft zweifeln ließ, ob ich dieses Projekt noch zu Lebzeiten abschließen kann. Also habe ich mir gedacht, ich konzentriere mich auf eine abgeschlossene Baugruppe und schaue mal, ob ich die fertigbekomme und wieviel Zeit ich dazu so brauche. Die Wahl fiel auf die Vorderachse. Da ich einige Teile davon in 3D „drucken“ lassen wollte, musste ich diese natürlich entsprechend detailliert modellieren. Hier haben mir die von Radi vor vielen Jahren zur Verfügung gestellten Bilder des Famo in Koblenz sehr gute Dienste erwiesen. Danke dafür nochmal.
Letztes Jahr habe ich also fleißig am Rechner modelliert, unendliche male Bilder durchsucht und vermessen. Dann war es soweit, ich habe ein paar Modelle bei Shapeways zum „Drucken“ gesendet. Warum Drucken in Anführungszeichen? Weil Shapeways seit einer Weile verschiedene Metalle anbietet. So z.B. Messing (Wachsausschmelzverfahren) und auch Stahl (Laser-Sintern). Als das Paket kam und ich die Teile ausgepackt habe, hats mich umgehauen. Ich war sehr begeistert von der Qualität der Teile und den Details. Die Stahlteile müssen noch zeigen, wie gut sie bearbeitbar sind (Lagersitze einbringen z.B.).
So, hier mal ein paar Bilder:
Original Vorderachse (Koblenz)
Mein 3D-Modell davon
Original (nicht in Koblenz)

Mein 3D-Modell davon
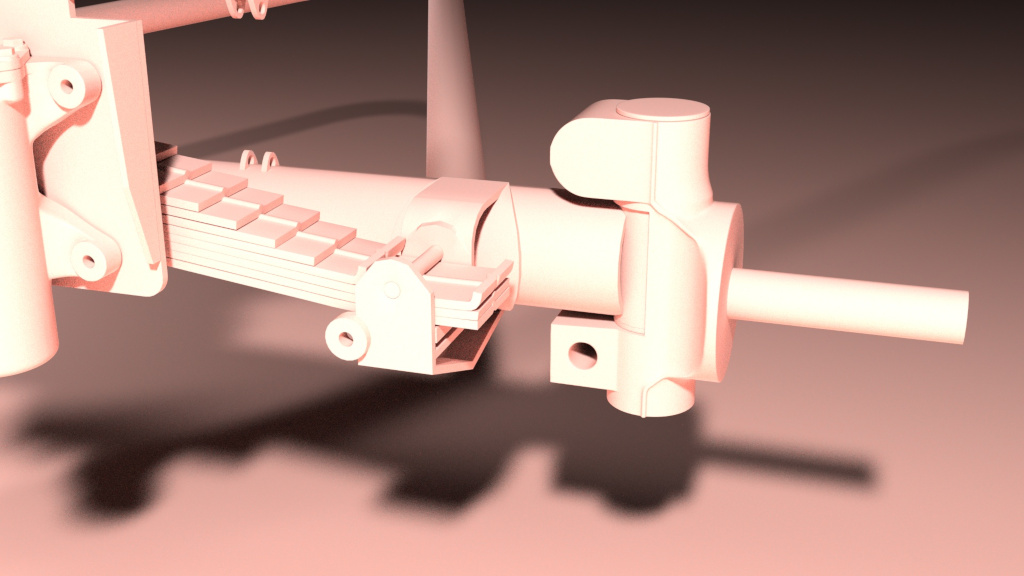
Original (nicht in Koblenz)
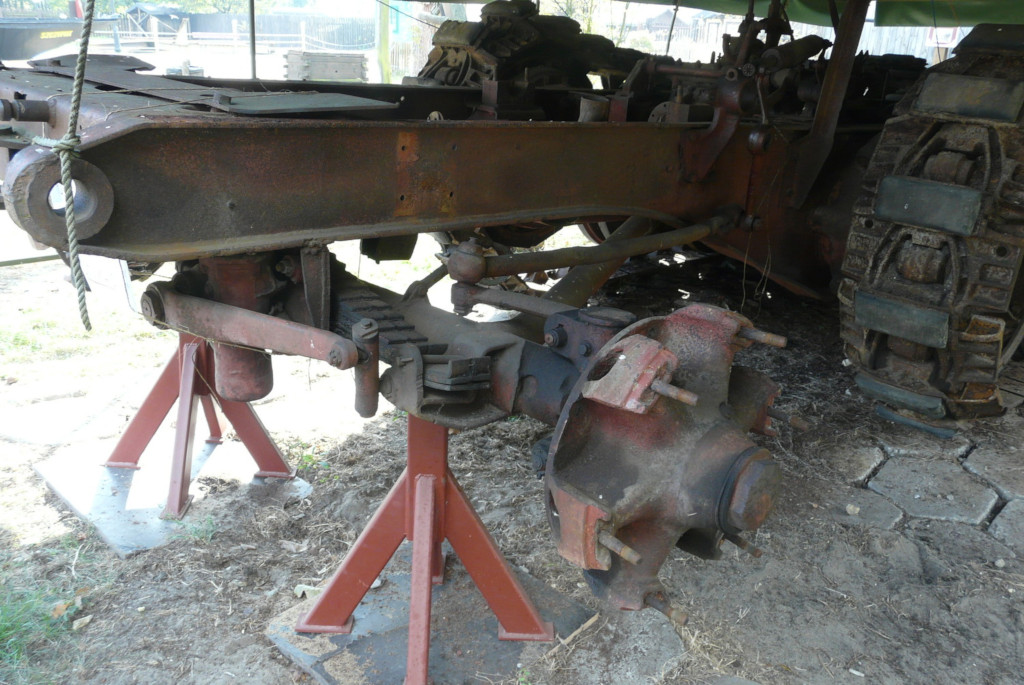
Mein 3D-Modell davon
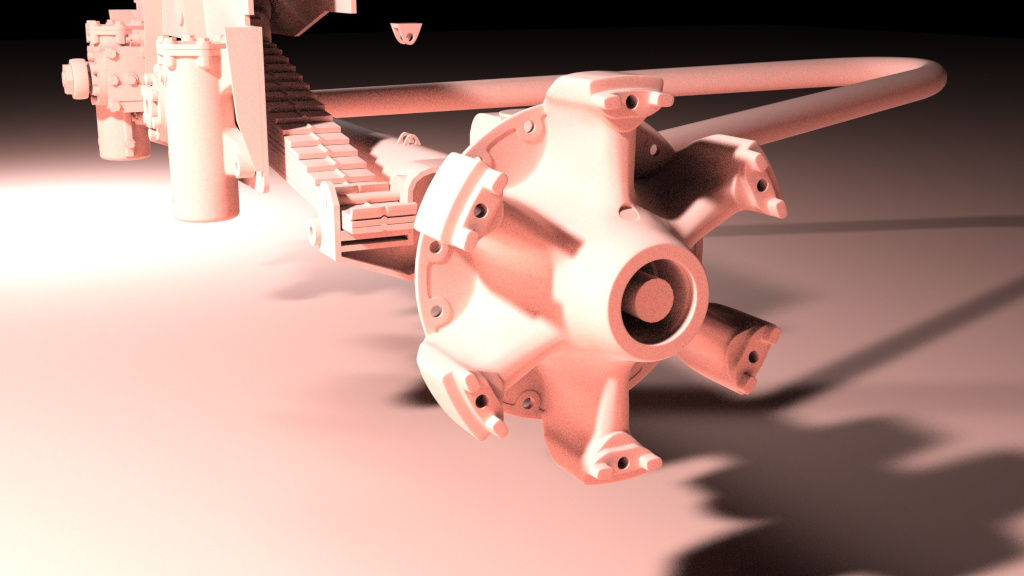
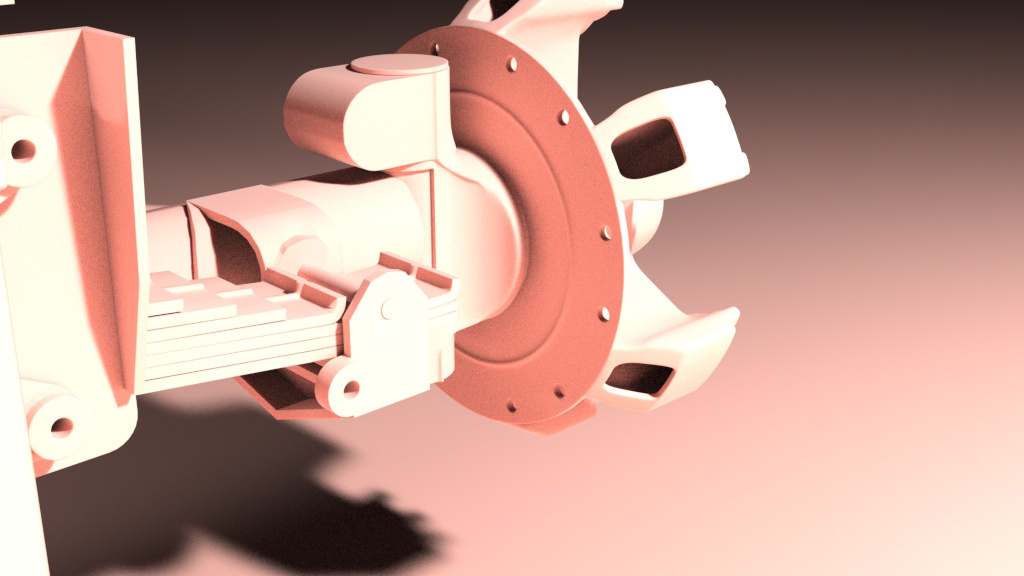
Und hier mal die Metallteile von Shapeways. Hier der linke Stoßdämpferbehältr mit Deckel aus Messing
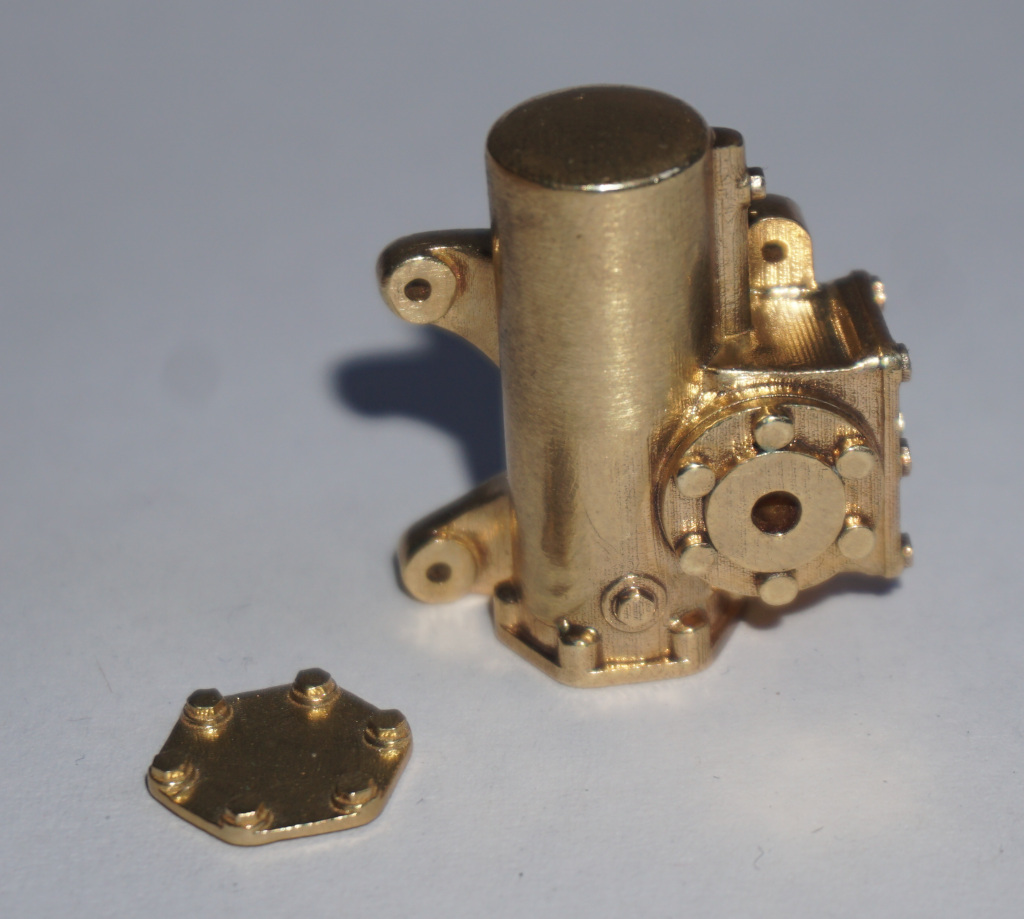
Selbst die Beschriftung konnte gut abgebildet werden.
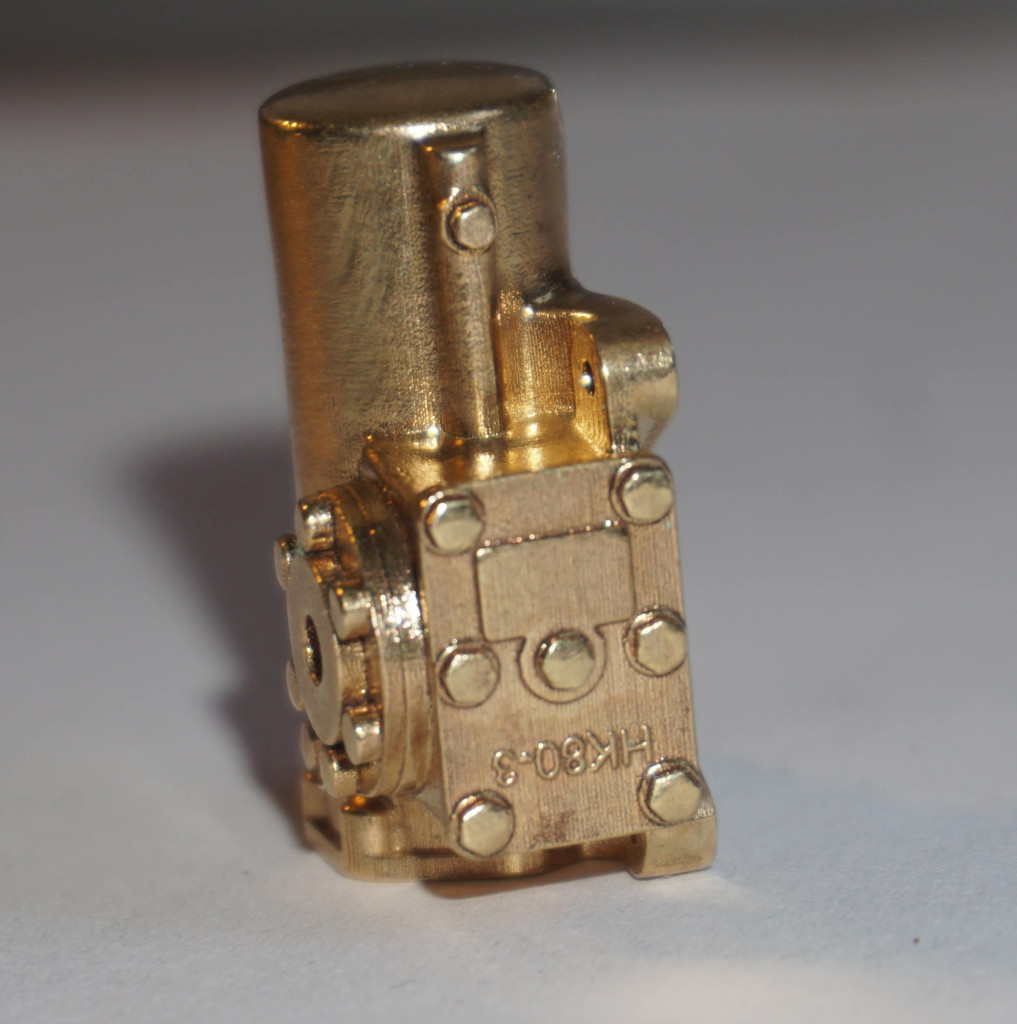
Hier mal ein Federhalter und Hebel für den Stoßdämpfer.
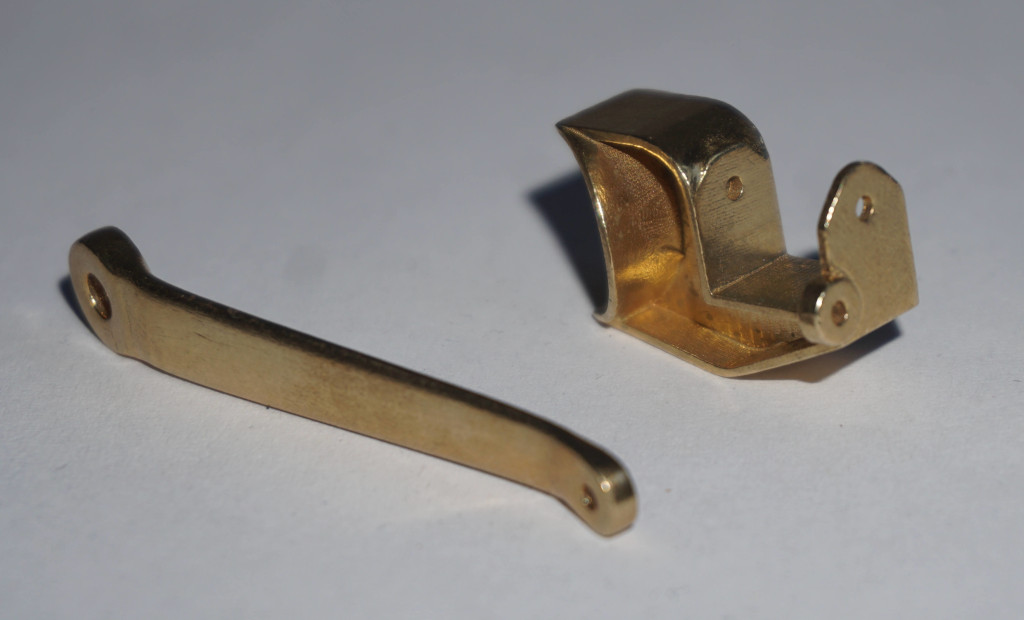
Hier die Felge aus Stahl (Laser-Sintern mit Bronzeauffüllung)
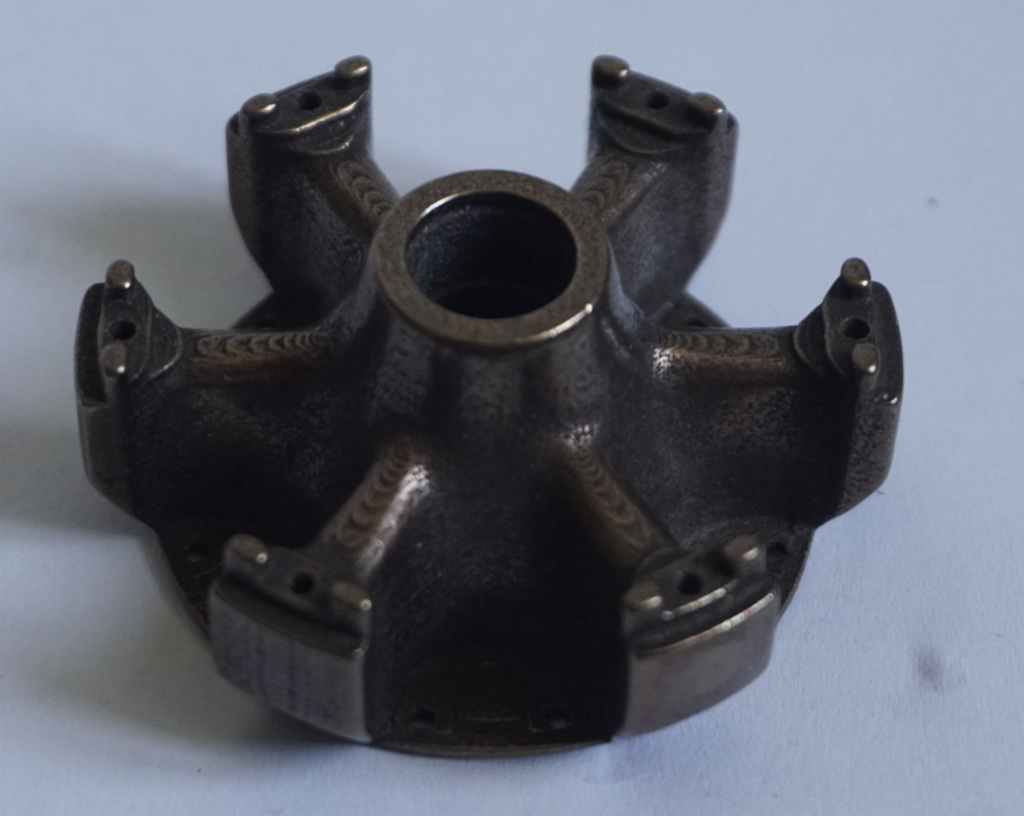
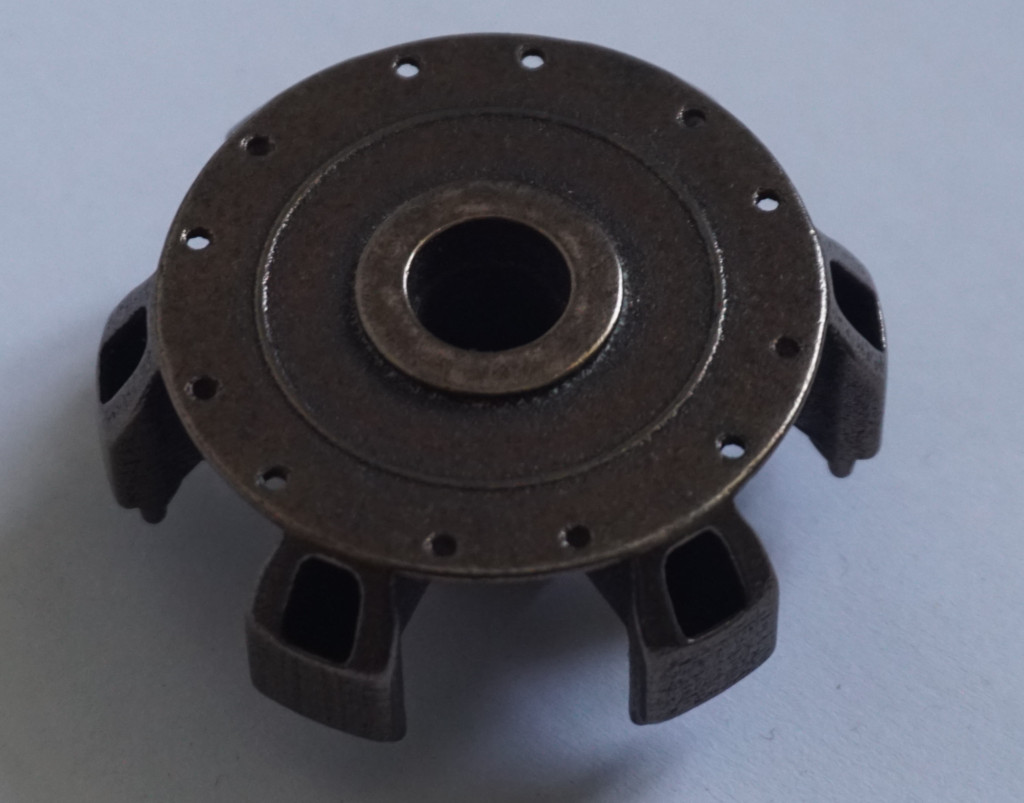
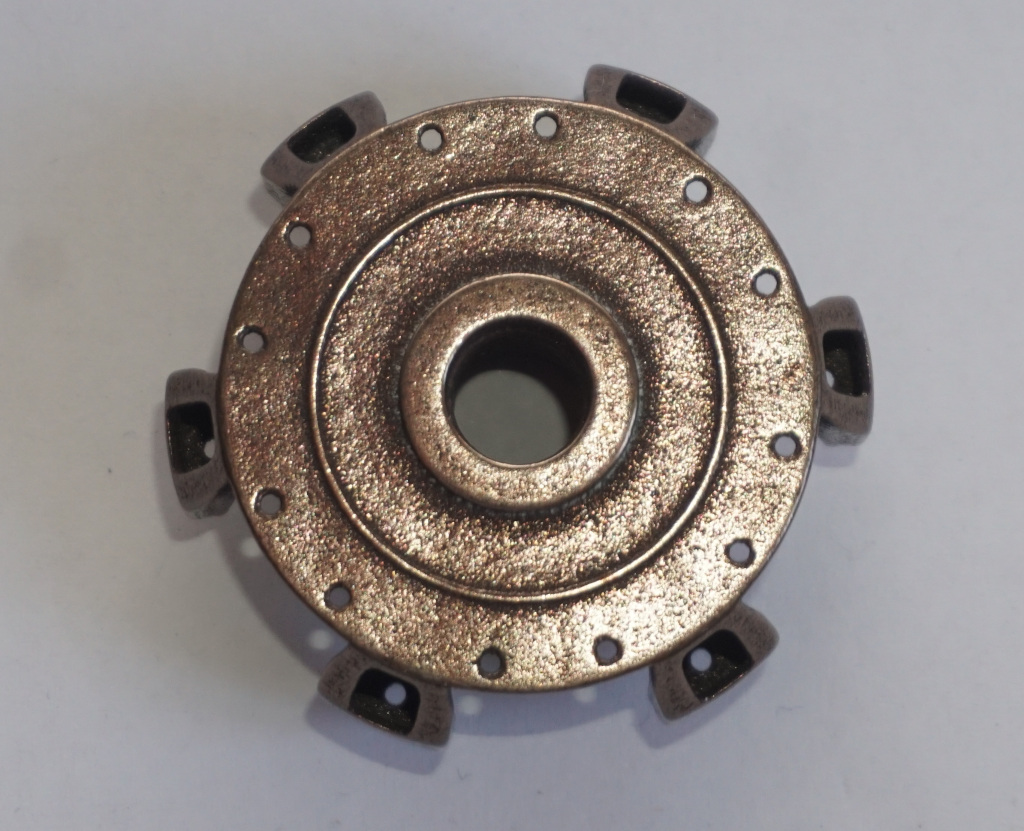
Und der Achsschenkel aus Stahl.
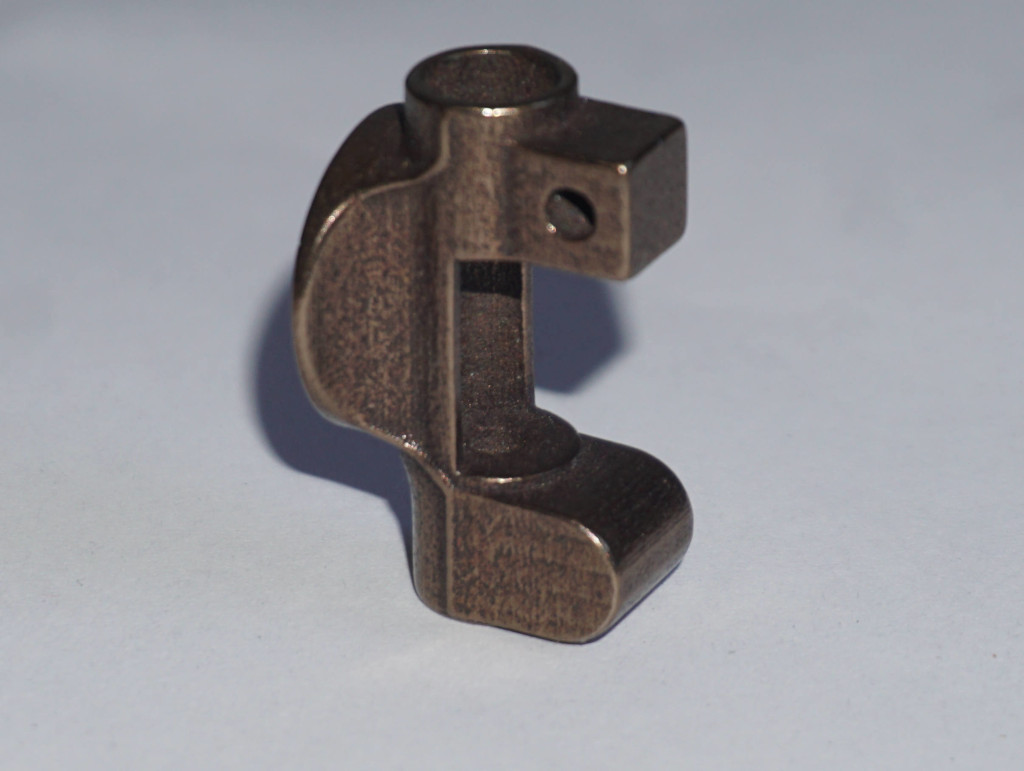
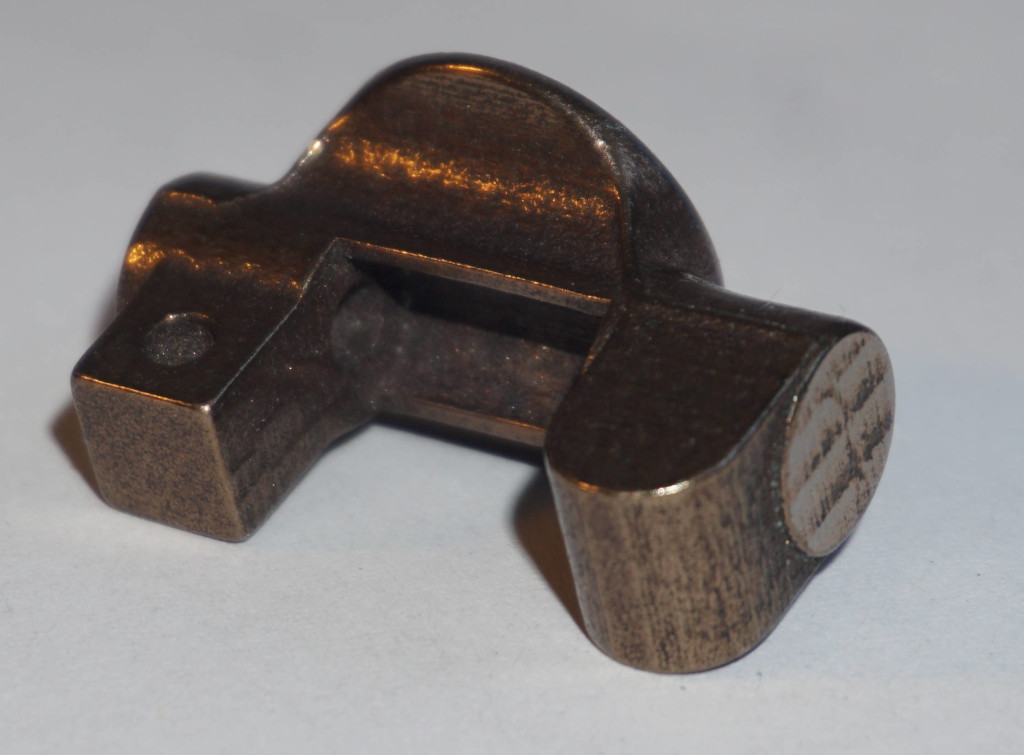
Zu den Preisen: Als ich das im Mai 2022 bestellt habe, kostete z.B. die Radnabe 30 EUR und der Federhalter 15 EUR. Das war ich bereit zu zahlen. Mittlerweilse haben sich die Preise sehr nach oben bewegt. Die Radnabe kostet jetzt 80 EUR.
Aktuell bin ich beim Anfertigen der Blattfeder. Davon recht bald mehr.
Ich hatte ja mal über ein Gemeinschaftsprojekt nachgedacht. Das kann ich nicht weiter so wie gedacht verfolgen, das bremst mich zu sehr aus. Ich kann aber allen Interessierten nach Absprache Daten, Modelle usw. zur Verfügung stellen. Die aktuellen Preise für die Teile bei Shapeways könnt ihr in meinem Shop dort verfolgen. Den habe ich zur Übersicht gemacht und nicht unbedingt zum Kaufen. Die Teile müssen ja noch beweisen, dass sie so passen und was taugen.
Shapeways
-- Grüße aus Leipzig
Matthias
www.boorad.de
|
|
|
|
|
06.06.2023, 18:45 Uhr
 paul182

|
hallo Matthias,
ein neuer Gipfel im Modellbau.
Atemberaubend!
Schwere Anerkennung!
Grüße, Reinhard
|
|
|
|
|
06.06.2023, 20:30 Uhr
 panzerpabst

|
Hallo Reinhard,
naja, bauen muss ich ja erst mal was
Trotzdem danke für deine Worte. -- Grüße aus Leipzig
Matthias
www.boorad.de
|
|
|
|
|
07.06.2023, 09:54 Uhr
 SLT50-2
Der Dachsmaster

|
Hallo Matthias ,
die Teile sehen absolut spitze aus
Ich drücke Dir die Daumen , dass das mit der Weiterbearbeitung klappt.
Grüße
Michael -- nicht´s ist unmöglich,wenn man es nur will
|
|
|
|
|
16.06.2023, 22:53 Uhr
 panzerpabst

|
Hallo zusammen,
Michael, Danke, mit der Optik der Teile bin ich wie gesagt sehr zufrieden. Wie du hier erfahren kannst, ist meine Maschine nicht länger blockiert und ich kann dann bald mal die Bearbeitung der Teile angehen.
Hier mal nun auch ein Beitrag, was ich neben dem Modellieren in 3D so am Projekt mache. Hier geht es konkret um die Blattfeder- ein „Drama“ in mehreren Akten … Es gab da verschiedene Varianten beim Famo. Die eine hatte flache Federn, welche mit Bändern zusammengehalten waren, die andere hatte keine solche Bänder sondern die Federn wurden durch ihr besonderes Profil übereinander gehalten. Die letzte Variante gab es auch noch mit angeschrägten Enden. Hier mal Bilder dieser Varianten.
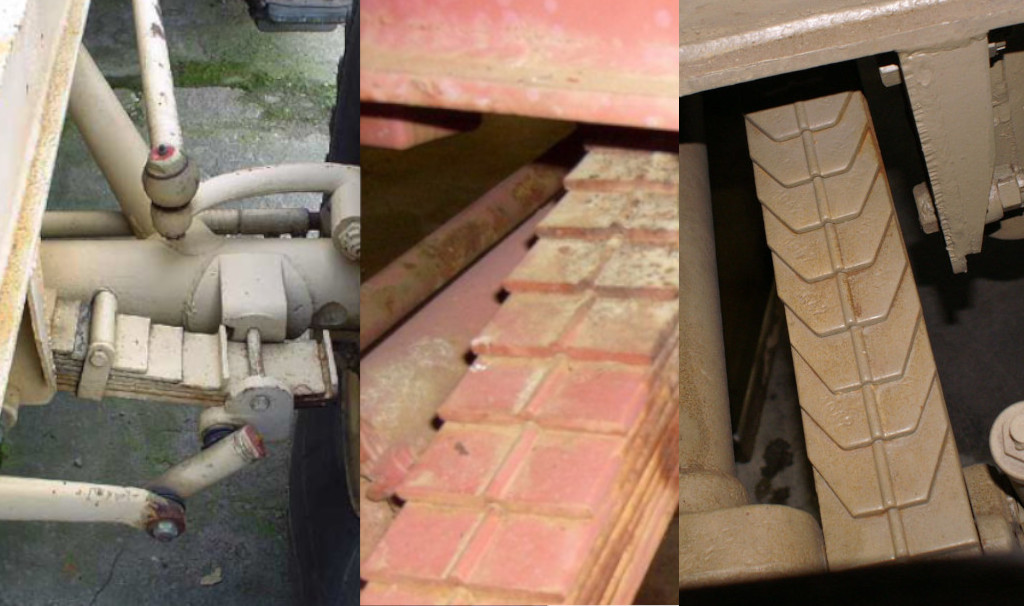
Natürlich habe ich mich für die komplizierte Variante entschieden (Bild ganz rechts). Also habe ich aus 1mm Messing bzw. Federbronze-Blech 9mm breite Streifen hergestellt (fragt nicht, solche unscheinbaren Arbeiten haben es in sich). Dann habe ich mir eine Art Meißel geschliffen und meine Fräsmaschine als Waagerechtstoßmaschine missbraucht um die Nuten zu fertigen. Hierzu habe ich weiterhin ein Holzblock als Schablone für die Streifen verwendet. Hier mal ein Video:
https://youtu.be/IXod5fmc7vg
Der Plan sah vor, die Nut 0,2 mm tief zu machen (hat auch erstmal geklappt) und dann durch Fräsen der Oberseite der Federn in der Mitte einen Steg von 0,2 mm Höhe stehen zu lassen. Diesen wollte ich dann mit einem weiteren entsprechend geschliffenen Meißel abrunden damit das Profil genau in die Nut passt. Und hier hing ich Monate fest da es einfach zu fitzelig war den Meißel genau hinzubekommen und dann auch noch exakt an dem Steg entlangzuführen. Das hat mich ewig blockiert (und meine Fräsmaschine auch weil ja dort alles schon genau eingerichtet war. Um diese Blockade zu lösen habe ich mich entschieden, den Steg wegzufräsen und eine Nut einzufräsen in die ich dann einen halbrunden Messingdraht löte. So sinnlos, die mühsam gefräste Oberseite wieder platt zu machen. Genauso ärgerlich, dass mir 2 mal der für die Nut verwendetet 0,8 mm Fräser abgebrochen ist. Beim 2. Mal schwöre ich, die Kinder haben inzwischen an der Tiefenzustellung gefummelt (der Kram steht ja bei mir in der Wohnung) und ich bin von korrekter Einstellung ausgegangen und habe munter losgekurbelt… Bei einem Preis von 15 EUR pro Stück nicht erfreulich. Zum Glück musste ich keinen 3. kaufen denn der 2. ist günstig abgebrochen und ich konnte ihn weiterverwenden.
Nach dem Ablängen der einzelnen Blattfederstreifen habe ich also an den Enden diese Nuten eingefräst und bin nun dabei, den halbrunden Messingdraht darin einzulöten. Pluspunkt: die Optik entspricht mehr dem Original (eine 0,2 mm hohe Erhöhung wäre zu wenig), Minuspunkt: die an den Unterseiten gefertigte Nuten waren zu flach. Ergebnis: viel Fummelei, Geschleife, Gefeile und Gefluche –aber es geht nun voran. Mit den bisherigen Ergebnissen bin ich recht zufrieden. Hier mal ein paar Bilder.
Hier sieht man das Profil ganz gut:
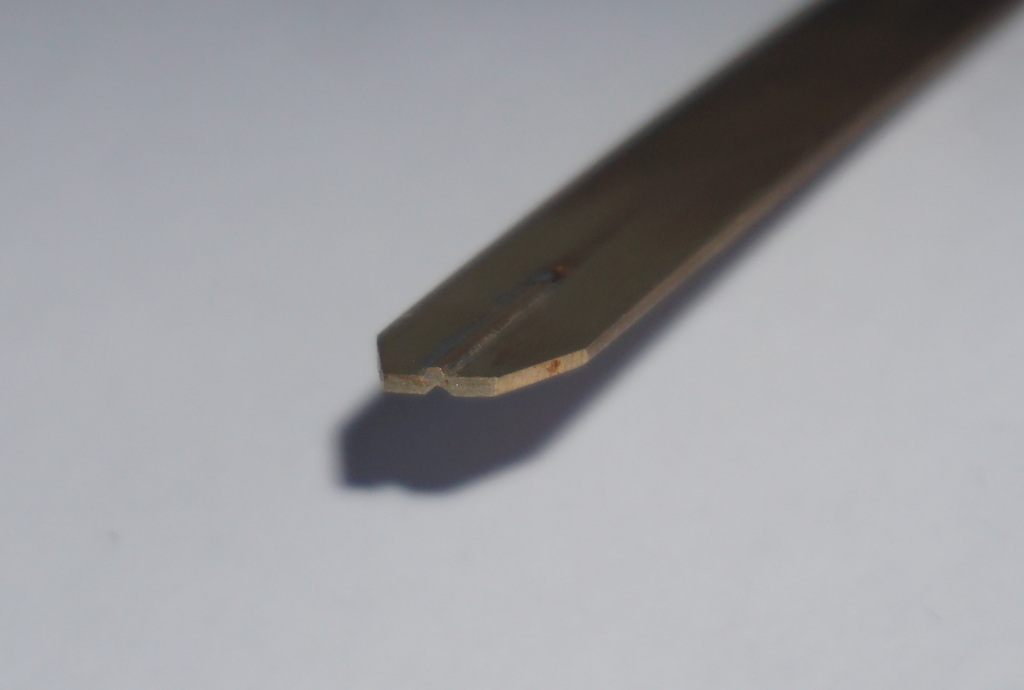
Hier mal die ganzen einzelnen Federn:
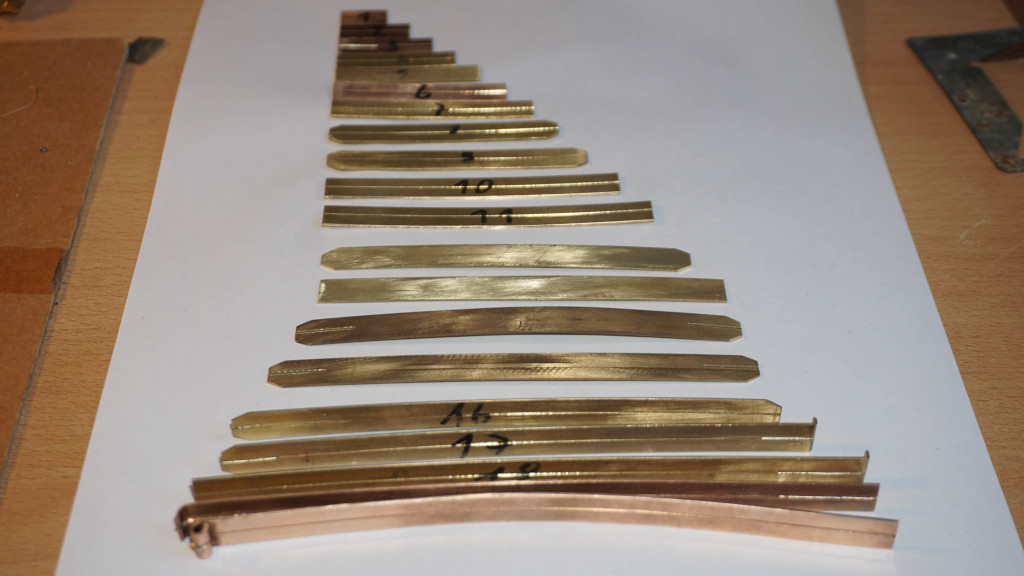
Um mal einen Eindruck zu gewinnen, habe ich mal das Federpaket zusammengestellt. Die oberen Federn sind noch nicht fertig:
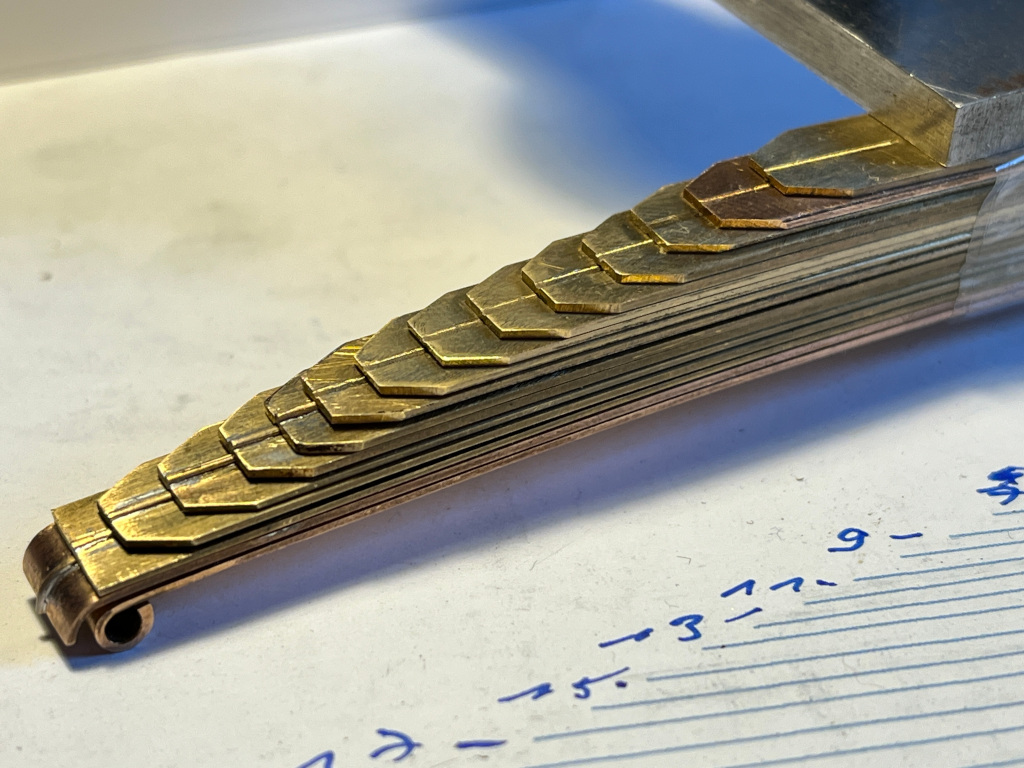
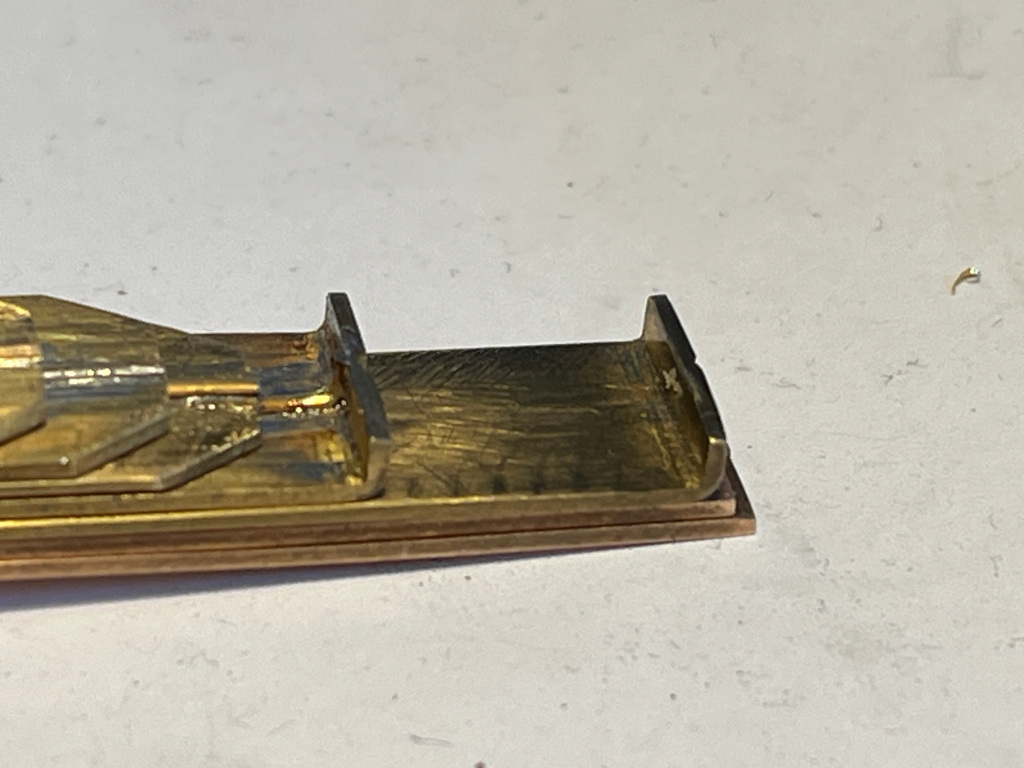
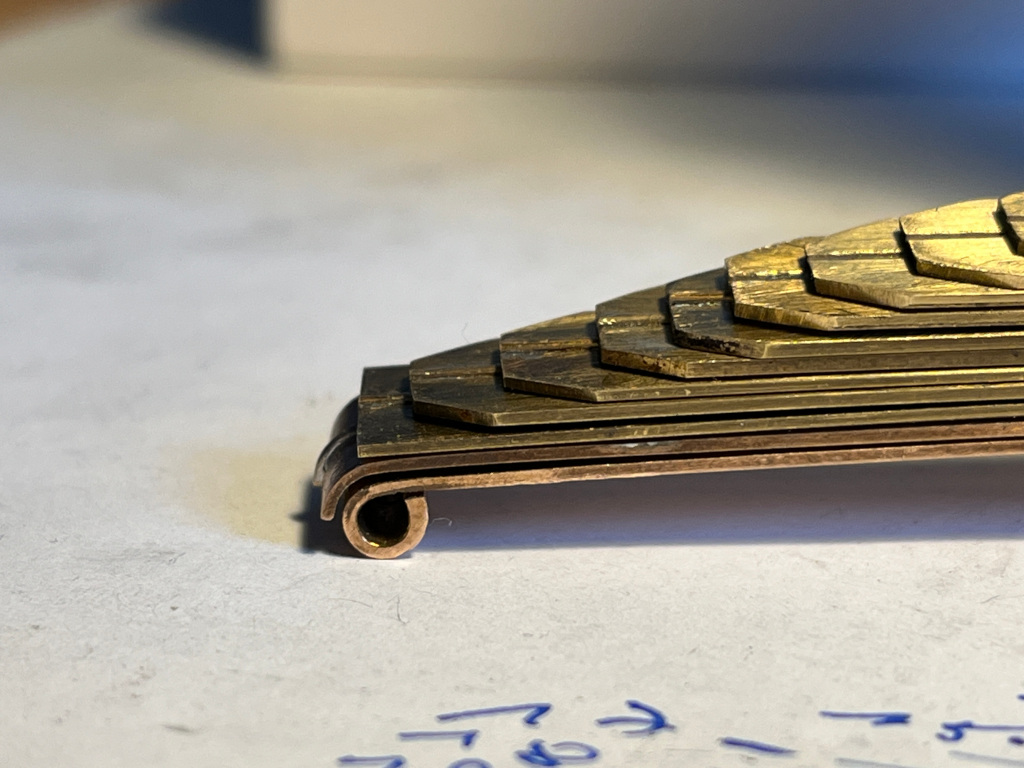
Damit alles dann richtig passt, müssen die einzelnen Federn natürlich noch gebogen werden. Das habe ich bei den untersten 3 schon gemacht, die anderen sind noch recht gerade - deswegen der Abstand beim nächsten Bild - hier habe ich keinen Druck auf die Feder ausgeübt:
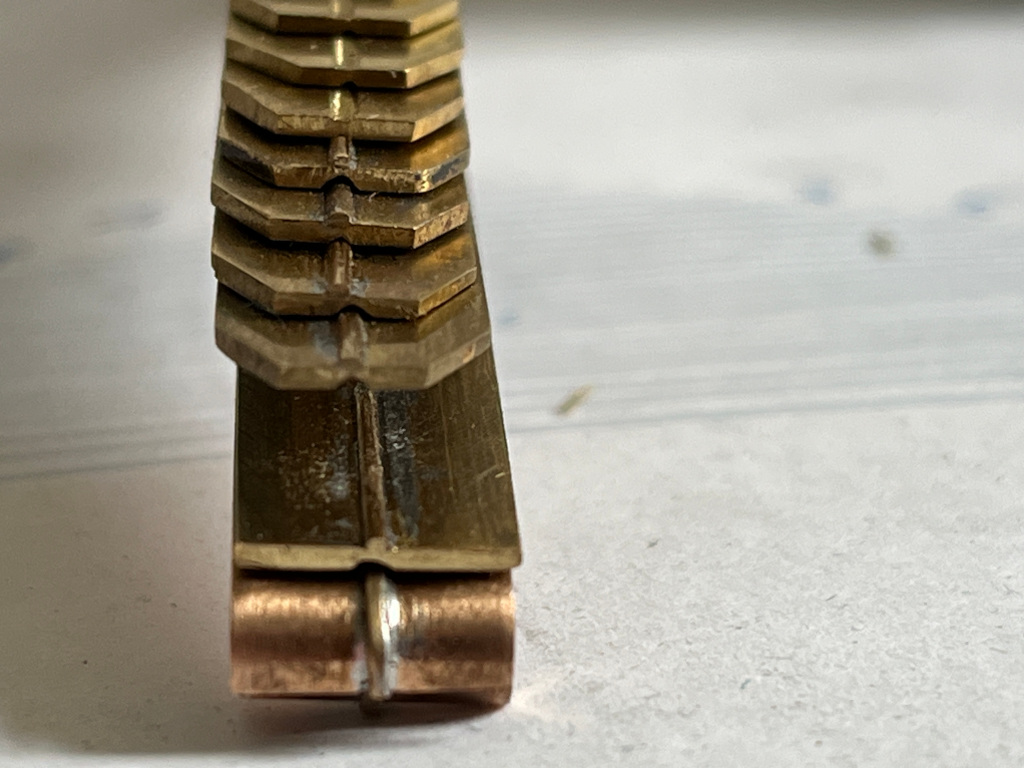
Das "Drama" hat sein Gutes, ich komme voran! Und irgendwie hat das Gefeile, Geschleife ja auch etwas Meditatives ...
--
Grüße aus Leipzig
Matthias
www.boorad.de
|
|
Beitrag 5 mal editiert. Zuletzt editiert von panzerpabst am 17.06.2023 11:06.
|
|
|
17.06.2023, 09:54 Uhr
 Leopold1A4

|
Servus Matthias,
sehr schön gezeigt wie man Federpakete bearbeitet (bearbeiten kann).
Hat mich sehr gefreut heute Morgen schon.
Was meinst, geht das Verfahren auch bei 1:16? Oder ist 1:10 schon klein genug?
-- _______________
Grüsse
Herbert
|
|
|
|
|
17.06.2023, 11:25 Uhr
 panzerpabst

|
Hallo Herbert,
schön, dass ich dir den Morgen versüßen konnte
Ich glaube bei 1:16 muss man da schon Abstriche bei den Details machen - da wären diese Federn ja auch nur knapp 6 mm breit. Das muss man echt wollen und sich auf echtes Gefummel einstellen. Was hast du denn konkret vor ?
Hier mal noch 2 Bilder von der Fertigung der einzelnen Federn.
Mit einer Schablone habe ich die Enden zum Abschleifen markiert (Proxxon Kappsäge KG50 mit Trennscheibe deren Seitenfläche ich hierfür nutze). Die abschließende Genauigkeit wurde dann mit Messchieber und Anschlagwinkel kontrolliert.
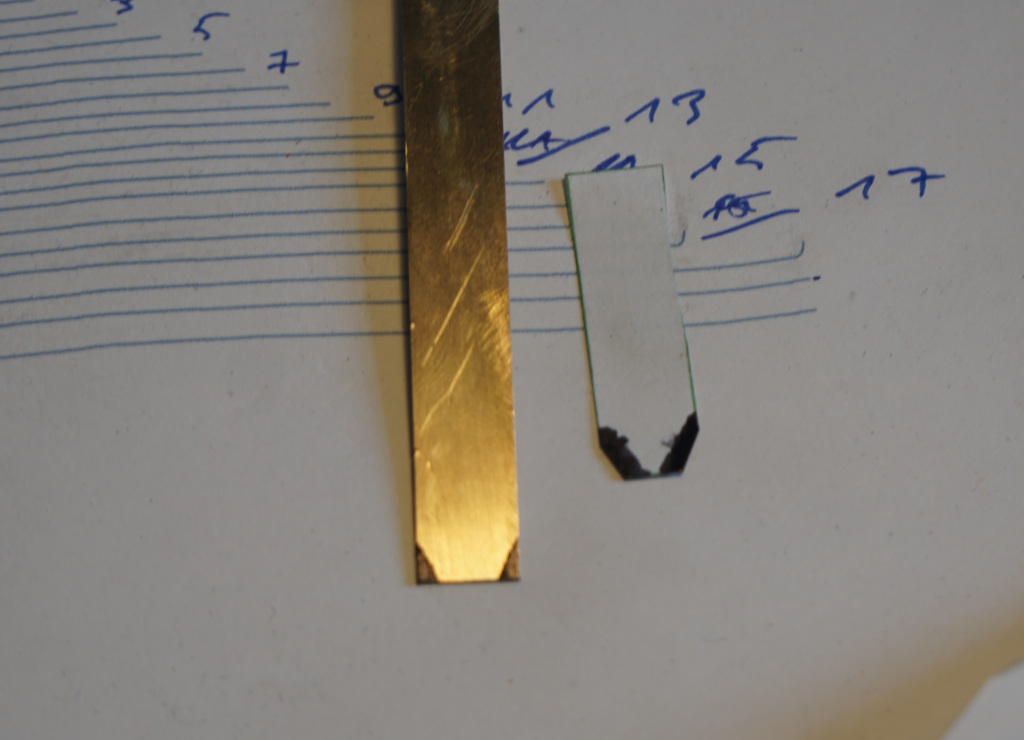
Und hier mal noch die verschiedenen Stadien der Bearbeitung.
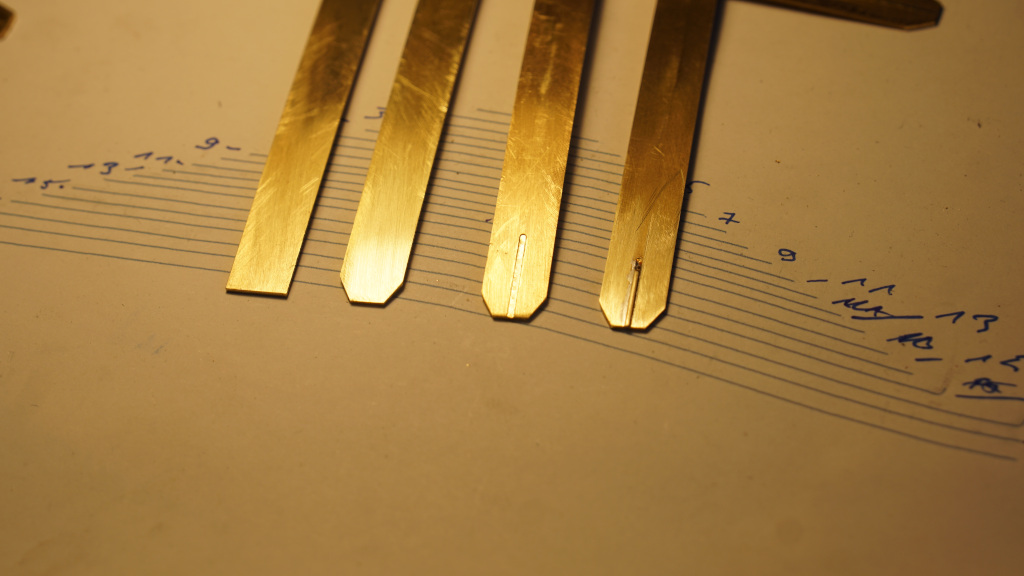
-- Grüße aus Leipzig
Matthias
www.boorad.de
|
|
|
|
|
18.06.2023, 08:32 Uhr
 Stahlsturm
(steelfire)
|
Schön daß es hier weitergeht, das ist einer der Nobelbauberichte mit denen sich dieses Forum von anderen abhebt.
Es war zwar zu erwarten, aber ich finde es schade schon jetzt mit Druckteilen gelangweilt zu werden, denn es wäre interessanter gewesen wie Du diese selbst gebaut hättest, was Du sicherlich auch gekonnt hättest.
Die Feder zur Vorderachse ist Dir gut gelungen. Hast Du die Öse wirklich so umständlich gebogen wie es in einem anderen Thema angedeudet wurde? Das flache Material mittels Vorrichtung einzuschieben und es so zu rollen. Ich verstand da den Aufwand nicht, sowas kann man doch problemlos über ein Stück Rundstahl wickeln.
Hast Du den Eindruck, daß die Feder durch die Verwendung von Messing wesentlich weicher wurde als durch den kompletten Aufbau mit Federbronce? Ich hätte die Befürchtung daß das Messing allmählich durch das Hin- und Herbiegen sich verfestigt und es genau so hart wird. Wobei der Federweg minimal ist und es dabei vielleicht noch nicht zur Kaltverfestigung kommt. Vielleicht müßte man mit einem niedriglegierten Aluminium diesen Effekt weniger fürchten.
Weiterhin frohes Schaffen und gutes Gelingen!
Falk
|
|
|
|
|